An EleFanT in the air
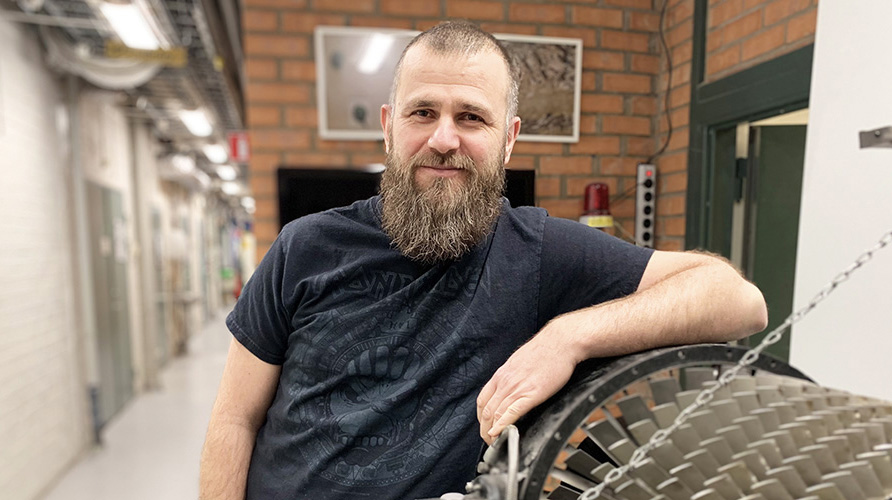
In the near future, the first commercial electric aircraft will take off from our airports. Maybe they will be driven by an electric fan instead of the conventional propeller – at least if the researcher Nenad Glodic gets his way.
The electric aircraft is just around the corner. Its development is faster than many people think. With the goal of Europe's aviation industry reaching net zero emissions by 2050, significant steps are taken in this area. Electric aircraft will operate on shorter distances to transport both goods and people within a few years. Long-haul flights with electric airplanes, on the other hand, take a while longer.
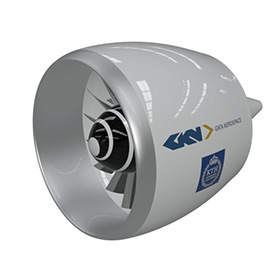
Not entirely unpredictable, KTH is in the game when the latest technology is developed. A group of researchers will, together with GKN Aerospace in Trollhättan, create an alternative to the propeller-driven planes which has been the common solution for propelling smaller electric aircraft.
”We are developing an electric ducted fan, which is advantageous from several perspectives. Above all, it makes less noise - most people who have flown in a propeller plane know that experience. It is also easier to integrate the fan engine on the fuselage, rather than being limited to the wing-mounted configurations. A fan that is protected by a nacelle is also safer in the event of an engine failure,” says Nenad Glodic , who leads the project research group at the Department of Energy Technology.
KTH's researchers are experts in how airflows interact with components and how to design, as in this case, fan blades so that they are as durable as possible. Nenad's group will compare fan blades made of composite and aluminum, among other things. Both are lightweight materials - every gram of every component counts on an airplane, especially when powered by electricity.
”We want to use the anisotropic properties of the composite, which means take advantage of the fact that the material has different mechanical properties in different directions. Composite is affected by how you lay the fibers, and by exploring this we can design an optimal fan blade that, for example, does not vibrate.”
The disadvantage of composites such as carbon fiber, Nenad explains, is that there is a brittleness in the material that makes it sensitive to impacts.. This is something you also have to take into account in the design.
Technologies for fuels and propulsion
Various technologies for fossil-free aviation are being developed worldwide, both for fuels and propulsion. Which solutions are most optimal depends on the size of the aircraft and how long distances they are expected to run.
”Batteries will probably have difficulty reaching the capacity, or rather the energy density, needed for the electric flights of the future, at least for medium and long-haul flights, if the development continues at the current pace. The most promising technology right now is hydrogen - either as fuel for a gas turbine engine or converted to electricity with the help of fuel cells. In our case, the electric fan will work regardless of whether the electricity comes from batteries or hydrogen-powered fuel cells.
Nenad's project is called EleFanT, which stands for Electric Fan Thruster, where the proposed plane is a regional aircraft with approximately 19 passenger seats. When we get to see KTH's electric fan motors in the air, Nenad Glodic secretly does not want to answer, but from a researcher's perspective, it is not far off in time.
"It is really fun to be involved from the beginning and influence the design of this type of components for the electric aviation industry."
The Elephant project, funded by the Swedish Energy Agency, started in July 2021 and spans 1.5 years.
Text: Anna Gullers