Predictive model control design for a small-scale steam engine based multi-source CHP system
Background
Steam power in general is unique when it comes to exploit different energy sources to produce combined electricity and heat (CHP). Typically, we associate steam power with large centralized power plant employing steam turbines for expansion of the steam. However, when it comes to small-scale steam power positive displacement expanders as a reciprocating piston engine is a better choice from cost/performance point of view.
RANOTOR corp. founded by the former project leader of SAABs steam engine project for car during the 70’s has developed a modern high tech steam engine that differ considerably from old classic steam engine system ( See figure 1).
The technology consists of several components that form a modern high tech steam engine system as shown in figure 2:
1. Burner for different fuel, e.g. biofuel, biogas, hydrogen, ammonia methanol etc.
2. Steam generator
3. Concentrating parabolic trough generating steam
4. The steam engine, axial piston engine for smooth and silent operation
5. Electric generator and electronic unit
6. Condenser (air or water cooled)
7. Feed pump
8. Steam Buffer (TES = Thermal Energy Storage)
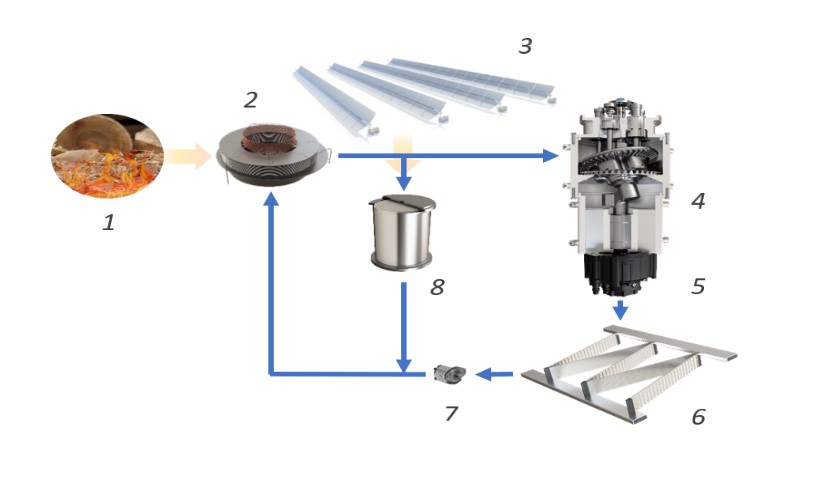
Heat sources will be concentrating solar thermal or/and different renewable fuels or waste heat. The steam generator (Boiler) is a once-through boiler with micro tubes. A steam engine with its inlet valve has an inherent quality to offer load following characteristics, which is an important characteristic for small-scale decentralized CHP and vehicle applications. As many of us know, steam powered car was a reality once in a time, and one example of a high performance steam powered car was Doble. During that time, they have succeeded to build control system that realized quick load following qualities.
The basic task for the control system is to establish a constant admissions (inlet) pressure and temperature even during fluctuation power demand and hence steam flow rate. Very basic, the feed water flow rate is changing to match the heat transfer rate from the energy source. Typically, pressure and temperature is measured and feed water flow, solar irradiation and fuel flow are synchronized to obtain the desired admission pressure and temperature. However, Predictive model control (PMC) could be possible to reduce adaption time of flow rates and realize a system with seamless operation characteristic. In addition, by utilizing a dynamic model-based control, it is possible to avoid unwanted power variations and thermal power supply and fluid mass flow imbalance in the steam boiler burner and feed pump causing low steam quality, low power etc.
This thesis work includes:
- Literature studies of old control system for automotive steam and stationary power plants of decentralized Rankine system size.
- Illustrate the level of complexity/simplicity necessary for this application and its consequences.
- Sensors that should be fitted to the steam expander (temperature, pressure, rotational speed/frequency, fluid mass flow etc).
- Conducting dynamic simulation of the control models with Simulink or other tools.
- Present a possible control model that can be tested and verified in the test rig at Maston lab in Skutskär
Prerequisites
To be applicable, the student should have adequate knowledge of heat transfer and thermodynamics. He/she should also be able to use MATLAB Simulink to conduct simulation work independently.
To apply send your CV together with University grades and expected starting date
Suggested Time Plan
Feb 2024 – Aug 2024 (open for change)
Contact Persons
Peter Platell , RANOTOR corp